I’m back from a month at the Archie Bray Foundation, where I did a month’s residency in studio, and presented a 3-day workshop. Great people in the workshop and at the Bray. Thanks for the good time and inspiration.
One of the things that came from this was exposure to Andrew Gilliatt. I’ve seen his
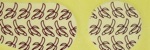
work in print, but it was more revealing to see him in studio. He’s using a Silhouette SD die-cutter to cut out adhesive paper resist shapes, and to cut out shapes from printed laser decal sheets to match his glazed or resisted areas. While I’ve known that the scrapbooking world had such devices, the light bulb didn’t really go on until I looked up the die cutters. Early models required cartridges from the manufacturers and only cut those shapes. Things got more sophisticated, and Silhouette America made a cutter that connects to your computer and will cut from .svg files: you can make your own or buy from Silhouette. The graphics are vector-based, like those created in Adobe Illustrator.
A post on Facebook about my interest in this technology yielded a kind note from Brenda Moore, former workshop participant, who mentioned that she’d taken a workshop at Sawtooth from Doris Petersham who included this technology. A note to Doris to ask if she had any pointers for info led to her suggestion of Make the Cut software as the most flexible tool to use with a die-cutter. The have a hardware connection with the Zing die-cutter.
I’m sure there are a lot of uses for die-cutting in ceramics. Before the scrapbooking movement in DIY, the plotter-cutters available were expensive tools more suited to business use, e.g. cutting the adhesive vinyl that galleries and museums use for shows, signs, etc. The low end of these seems to about $900.00 and up from there. One of the U.F. faculty in painting who does works with icons and symbols has a wide-bed plotter-cutter. Since, there has been development of smaller, less expensive home units which are more within the reach of individuals. I plan to cut shapes from paper for use as stencils on leather-hard clay. I’ve always loved doing slip work on leatherhard clay, but it requires more timing pressure than majolica on bisque ware. This year on sabbatical, I plan to take some time to investigate the die-cutter and slip work, and will write this up when I’ve learned more. Another curiosity is cutting shapes from solid sheets of laser or China-paint decals. Chinese Clay Art now offers sheets of solid decal color. This is GREAT if you want to make something like graphic stripes, etc., and the die-cutter will expand what can be easily cut from such sheets (once I learn more …. )
I bought the cheapest Silhouette – the Silhouette Portrait. It has optical registration, is similar to their CAMEO but smaller – 8″ cutting width. It just arrived yesterday, and I’m working on setting it up. This really all was instigated by ceramic artist and educator Martina Lantin asking me to do the next Crimson Laurel Gallery themed cup show, Natural Disaster. I wanted to use symbols and icons to represent natural disaster suggestions, either in slip or decal color shapes.
Once I discovered Make the Cut and the Zing, thanks to Doris’s kind help, I wanted one of those. One is on the way. The Zing will do 14″ wide cuts, online reviews say it’s better for thick or tough materials (e.g. Tyvek for re-usable stencils), and has laser registration, which should be more accurate. Make the Cut works with many die-cutters and offers a lot of tutorials and free Webinars on Tuesday nights. The Zing people are kindly facilitating my research, and I hope to see my new Zing soon. I’ll post more info here on the blog as I learn, and will eventually work on an article and a handout for my web site.
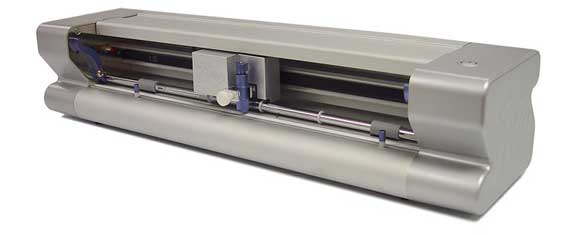